Fracture mechanics is a branch of engineering and materials science that deals with the study of how materials behave when subjected to stresses that lead to the formation and propagation of cracks or fractures. It provides a systematic framework for understanding the behavior of materials in the presence of defects and cracks, with the ultimate goal of predicting and preventing failure.
The study of fracture mechanics has become increasingly important in various industries, including aerospace, civil engineering, mechanical engineering, materials science, and more. It has led to advancements in designing safer and more reliable structures, components, and materials.
Types of fracture
Fractures can be classified into different types based on their characteristics and the behavior of materials when subjected to external forces. The two primary categories of fractures are brittle fractures and ductile fractures.
Brittle Fracture
Brittle fractures occur in materials that exhibit little to no plastic deformation before failure. They typically happen suddenly, without much warning. Some key points to consider:
Practical Example: One practical example of a brittle fracture is the shattering of glass. When a glass object is subjected to a sudden impact or stress beyond its capacity, it fails catastrophically, resulting in fragments. This behavior is due to the atomic structure of glass and its inability to undergo significant plastic deformation.
Characteristics: Brittle materials, such as certain ceramics and some polymers, have a limited ability to deform plastically. When stress is applied, the material tends to fracture without appreciable deformation. The fracture surfaces of brittle materials are often smooth and feature little energy absorption.
Applications: Understanding brittle fracture is crucial for the design and safety of structures and components. For example, in civil engineering, when designing a bridge, it is essential to consider the potential for brittle fractures in materials like brittle concrete. Careful material selection and reinforcement can help prevent brittle failures.
Ductile Fracture:
Ductile fractures occur in materials that exhibit significant plastic deformation before failure. These materials can withstand high strains before ultimately fracturing. Here are some important points to consider:
Practical Example: Imagine a metal wire being gradually pulled until it breaks. Initially, the wire undergoes plastic deformation, thinning in the region where the stress is applied (known as necking). Eventually, the wire reaches its ultimate strength, and further deformation leads to rupture. This example demonstrates the behavior of ductile materials.
Characteristics: Ductile materials, such as most metals, can undergo substantial plastic deformation before fracture. They exhibit necking, where the material thins locally while elongating. Ductile fractures often feature rough and torn surfaces, indicating the energy absorption during the deformation process.
Applications: Ductile materials are commonly used in engineering structures due to their ability to absorb energy before failure. For example, in the automotive industry, the use of ductile materials like steel in car frames helps to absorb energy during collisions, protecting the occupants. Ductile behavior is also critical in manufacturing processes like forging and metal forming.
Different modes of fracture ?
When studying fractures, it is important to understand the different modes of failure. Fracture modes describe how a material or structure fails under specific loading conditions. The three primary modes of failure:
Mode I – Tensile or Opening Mode
Practical Example: Imagine a piece of paper being pulled apart. As the force is applied in opposite directions, a crack develops, propagating perpendicular to the applied force. This is an example of Mode I failure.
Description: Mode I failure occurs when a crack or fracture propagates perpendicular to the direction of the applied tensile or opening stress. It is characterized by the separation of material along a plane, resulting in a gap or opening. Mode I is the opening mode and the displacement is normal to the crack surface.
Applications: Mode I failure is commonly observed in structures subjected to tension, such as ropes, bolts, or beams under bending. Understanding this mode is crucial in assessing the safety and integrity of structures under tensile loading.
Mode II – Shear or Sliding Mode:
Practical Example: Visualize two wooden blocks stacked on top of each other and a force being applied parallel to their surface. As the force exceeds the material’s strength, a crack forms and propagates parallel to the applied force. This represents Mode II failure.
Description: Mode II failure occurs when a crack or fracture propagates parallel to the direction of the applied shear stress. It involves sliding or shearing of the material along the crack surfaces. Mode II is a sliding mode and the displacement is in the plane of the plate—the separation is antisymmetric and the relative displacement is normal to the crack front.
Applications: Mode II failure is relevant in structures where shear forces are present, such as the delamination of composite materials, adhesive failures, or the sliding of geological formations along fault lines.
Mode III – Tearing or Torsional Mode:
Practical Example: Imagine holding a cylindrical rod and twisting it at the ends in opposite directions. As the torsional stress increases, a crack forms and propagates perpendicular to the applied torsional force. This represents Mode III failure.
Description: Mode III failure occurs when a crack or fracture propagates perpendicular to the plane of the applied torsional stress. It involves tearing or twisting of the material along the crack surfaces. Mode III also causes sliding motion but the displacement is parallel to the crack front.
Applications: Mode III failure is relevant in structures to torsional or twisting loads, such as shafts, gears, or rotating components. Understanding this mode is important for assessing the failure mechanisms and designing against torsional failure.
Conclusions
Fracture mechanics stands as a pivotal discipline at the intersection of engineering and materials science, unraveling the intricate behavior of materials when subjected to forces that give rise to fractures and cracks.
Some of the key points are as follows:
- By understanding the failure modes, engineers and researchers can analyze fracture behavior, predict failure mechanisms, and design structures to prevent catastrophic failures.
- Considering the specific failure mode when evaluating the safety and integrity of materials and structures under different loading conditions is crucial.
- Fracture mechanics aids in identifying failure modes like brittle fractures, ductile fractures, fatigue failure, and stress corrosion cracking.
- The discipline involves materials testing, safety considerations, numerical simulations, and design enhancements to ensure the integrity of structures and components.
- Brittle fractures exhibit rapid, sudden failure with little plastic deformation, while ductile fractures involve significant plastic deformation and energy absorption.
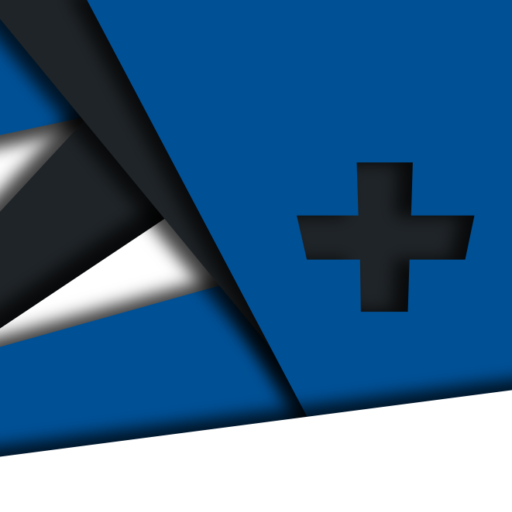
Android Apps
⭐️ ⭐️ ⭐️ ⭐️ ⭐️ 1000+ | 400,000 + Downloads (Cumulative)
At eigenplus, our goal is to teach civil engineering students about structural analysis and design starting from the fundamental principles. We do this with the help of interactive android applications and accompanying web articles and videos.
Our apps have helped more than 400 thousand students across the world to understand and learn the concepts of structural engineering. Check out our apps on the google play store.
This article was crafted by a group of experts at eigenplus to ensure it adheres to our strict quality standards. The individuals who contributed to this article are:
Author
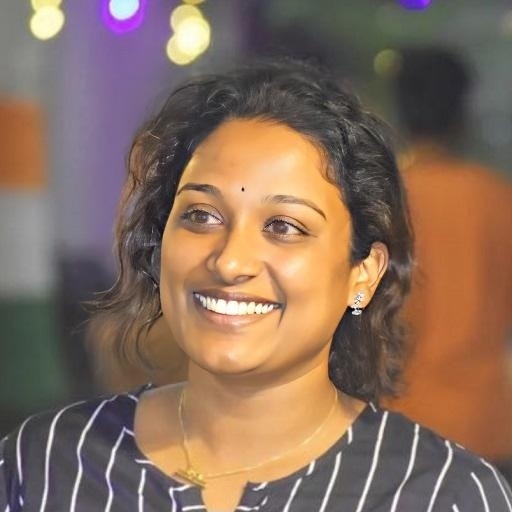