Can you answer how a white chalk stick will break when you apply load in an axially outward direction? Do you know the difference between various stress strain curves? Do you know what is the difference between the stress strain curves of mild steel in compression and in tension? You can answer all these questions by reading this small post. So let’s get started.
When we start learning about any material, one of the first steps is to learn the load vs deformation curve of that material specimen. To make this process cross-section free, we study the stress strain curves. The same material shows different behavior under different types of load conditions. We have listed a few important observations in the stress strain curves of mild steel under tension in our previous blog post. In this article, we are going to summarize a few more stress strain curves related to brittle and ductile materials. So let’s take out each one by one.
Stress strain curves for Mild steel in compression :
- Mild steel under compression will have the same modulus of elasticity as that in the tension. It will also have approximately the same yield stress Fy.
- The initial region of the stress strain curve in compression is very similar to that of tension.
- On further increasing the stress, the sides of the sample will bulge outward and will become barrel-shaped like shown in the figure below.
- There is no necking under compression testing like in tension testing.
Some other points worth noting:
- If we increase the grade of steel, Its strength will increase but ductility will decrease.
- The modulus of elasticity for different grades of steel will remain constant.
- While drawing the stress strain curves for Aluminum and Copper, Yield point is not clear. So we use the offset method to calculate the yield point.
- 0.2% proof stress is taken as Fy for calculation
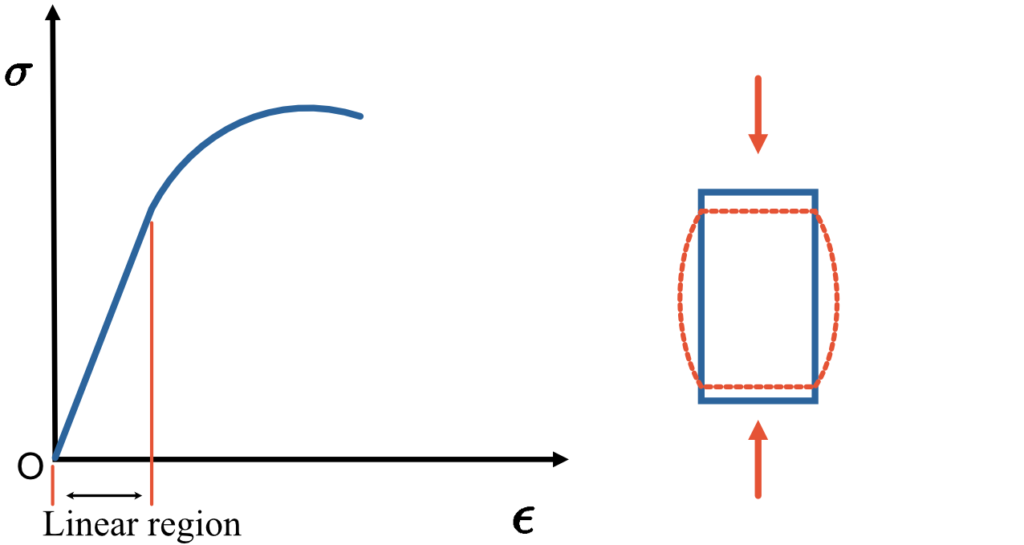
Stress strain curves for Brittle material:
- There is no plastic zone for brittle material.
- Brittle material like cast iron gets fractured at very small strain.
- In tension, the Failure plane is perpendicular to the longitudinal axis because the fracture is due to normal stress and normal stress is maximum at 90 degrees.
- There is very less reduction in the area before failure.
- The linear elastic range in compression is larger as compared to that in elongation. However, the modulus of elasticity is the same for both, in tension testing and in compression testing.
- Brittle material is stronger in compression as compared to that in tension. This is on account of microscopic cracks already present in the brittle material which elongate during tension and leads to early fracture. In compression, Microscopic cracks are breezed leading to greater strength in compression.
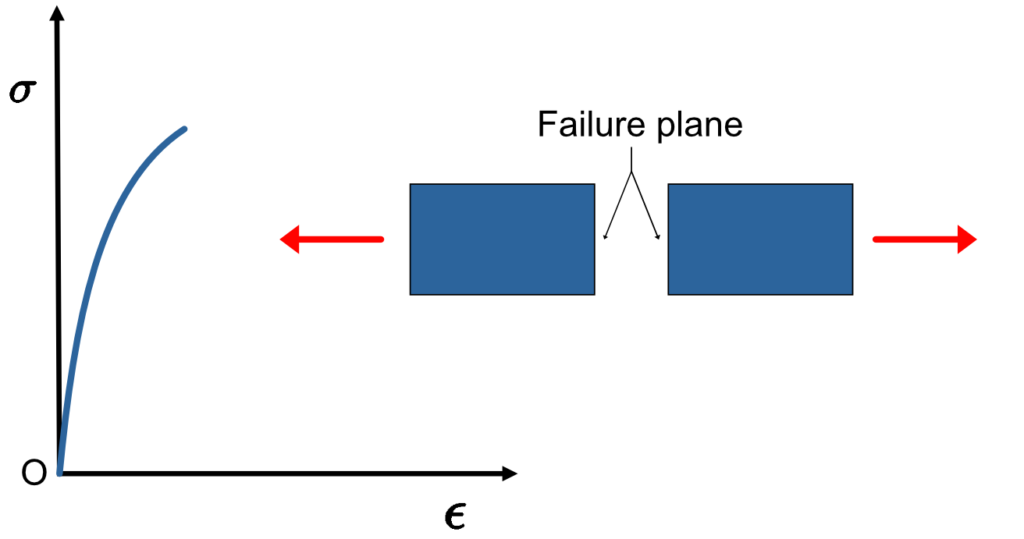
Some other points worth noting:
- When a ductile material is subjected to torsion, the failure plan will be at 90 Degree because on that plane, shear is maximum and ductile material fails due to shear.
- When brittle material is subjected to torsion, the failure plan will be at 45 Degree because on that plan, normal stress is maximum and brittle material fails due to normal stress. Experiment with this on a chalk stick. Results will be fun to note.
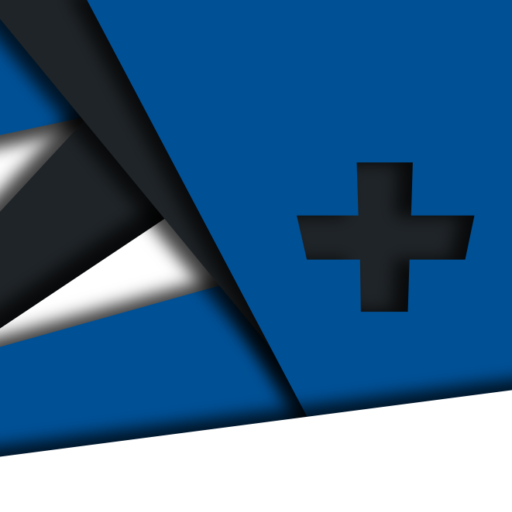
Android Apps
⭐️ ⭐️ ⭐️ ⭐️ ⭐️ 1000+ | 400,000 + Downloads (Cumulative)
At eigenplus, our goal is to teach civil engineering students about structural analysis and design starting from the fundamental principles. We do this with the help of interactive android applications and accompanying web articles and videos.
Our apps have helped more than 400 thousand students across the world to understand and learn the concepts of structural engineering. Check out our apps on the google play store.